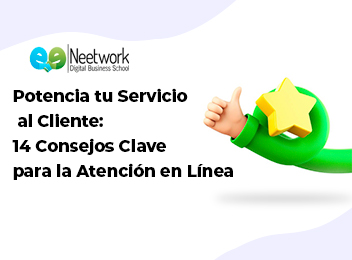
El concepto de las 5S, un sistema de organización y gestión para mejorar la productividad y el entorno laboral, tuvo su origen en Japón. Se desarrolló en Toyota y se le atribuye su nacimiento en la fábrica de automóviles de la compañía. Aunque las bases de las 5S existían antes, la adopción y formalización de este sistema de trabajo se consolidó y popularizó en la década de 1960 como parte del enfoque de gestión y mejora continua conocido como "lean manufacturing" o "producción ajustada".
Descubre más sobre su implementación y cómo beneficia a los trabajadores física y mentalmente en este artículo
Aplicar estrategias efectivas es fundamental para el éxito de una empresa por varias razones:
Contenido del artículo
Las 5S representan un método laboral para optimizar la productividad mediante la organización y limpieza en los lugares de trabajo. Este enfoque japonés aborda 5 aspectos que se relacionan con la letra 'S', facilitando su recuerdo e implementación. Cada uno de estos pasos contribuye a identificar y eliminar obstáculos a la productividad.
Su gran ventaja radica en su aplicabilidad a cualquier industria, independientemente de su tamaño, sin necesitar informes extensos ni grandes inversiones iniciales. Considerado como el punto de partida del lean manufacturing, esta metodología cultiva la mejora empresarial con prácticas sencillas pero efectivas. A pesar de su sencillez, su metodología resulta efectiva.
Su enfoque se centra en la organización, limpieza y mantenimiento del espacio de trabajo, fomentando hábitos a largo plazo. Este proceso facilita la localización de herramientas, previene accidentes y promueve la responsabilidad entre los trabajadores.
El principal propósito de la metodología de las 5S es instaurar un entorno laboral organizado y seguro, con el fin de sentar las bases para una disciplina que propicie la mejora continua en el ámbito empresarial. Para lograr este cometido, esta metodología busca alcanzar los siguientes objetivos:
Por "desperdicios", nos referimos a aquellas actividades o procedimientos que obstaculizan la eficiencia. Entre los más frecuentes se incluyen la sobreproducción, el exceso de inventario, productos o materiales en desuso que ocupan espacio en almacenes, así como defectos que demandan esfuerzos adicionales para su corrección y periodos de inactividad a la espera de piezas o información.
La eliminación de los desperdicios conlleva una notoria mejora en la productividad. Al contar con los materiales adecuados, las herramientas correctas en su lugar correspondiente y un equipo preparado, se evitan demoras y labores previas antes de iniciar las tareas, permitiendo realizar más en menos tiempo.
Un entorno limpio y organizado en el lugar de trabajo reduce las posibilidades de accidentes, como caídas o golpes por objetos, que suelen ser más comunes de lo que se piensa. Además, este ambiente influye en el bienestar de los trabajadores al tener acceso a lo necesario de manera inmediata, disminuyendo así el estrés durante las labores.
Esta metodología capacita a los individuos para llevar a cabo acciones y considera sus sugerencias para optimizar los espacios. De esta manera, se logra una mayor participación y compromiso por parte de los trabajadores tanto en la calidad del trabajo como en la responsabilidad de mantener la empresa limpia y ordenada.
Seiri se enfoca en revisar todos los elementos y procesos para identificar los indispensables en la realización de las tareas. Cualquier herramienta o instrucción sin una función clara debe ser eliminada.
La persona a cargo de las 5S evaluará las estaciones de trabajo y etiquetará con un color aquellos elementos innecesarios. Si no son relevantes, se determinará su utilidad y si es necesario conservarlos.
Una vez identificados los elementos esenciales, se procede a organizarlos. La premisa es "un lugar para cada cosa y cada cosa en su lugar", asegurando un almacenamiento sistemático para que todos en el equipo sepan dónde encontrar lo necesario.
El uso de carpetas, organizadores y sistemas de almacenamiento facilita la organización. Es crucial ubicarlos en lugares accesibles para agilizar la búsqueda de artículos sin perder tiempo.
La limpieza de espacios, herramientas y equipos laborales impacta la seguridad al reducir accidentes. Mantener máquinas limpias y en funcionamiento adecuado previene daños que puedan afectar la producción.
Garantizar suministros de limpieza dentro de las instalaciones para el acceso de todos.
Esta etapa mide el progreso y busca mantenerlo, estableciendo reglas y bases para la ejecución de las acciones.
Crear manuales, horarios, listas y métricas ayuda al equipo a mantener las condiciones ideales de orden y limpieza.
La disciplina es clave para el funcionamiento continuo del método. Se refiere al compromiso de realizar tareas sin necesidad de supervisión, convirtiéndose en parte de la cultura de la empresa.
Realizar auditorías para verificar que se cumplen los pasos acordados, convirtiéndolos en hábitos.
Las 5S se complementan con herramientas de lean manufacturing como kanban, kaizen, poka yoke, con el fin de crear entornos laborales más seguros y productivos, optimizando los recursos al máximo. Esta metodología es ampliamente utilizada en diversas industrias, desde la manufactura hasta la educación, buscando reducir desperdicios y potenciar la fuerza laboral para mejorar la calidad de los espacios. Su aplicación ofrece beneficios significativos en la planificación estratégica de cualquier negocio.